Formation Mechanism And Control Of Flaring In Forward Tube ...
- PDF Analysis of tube spinning process - ResearchGate.
- 6.9 Synthetic Fibers - US EPA.
- [PDF] Experimental results and mathematical formulation of.
- PDF Engineering Techniques of ring Spinning - ResearchGate.
- PDF RING SPINNING | ders deers - A.
- Cotton Yarn Spinning Process Step by Step - Textile Learner.
- PDF The Rieter Manual of Spinning.
- PDF Spinning Basics 1 of 7.
- Spinning Process Overview: From Fiber Material to Yarn.
- Spinning - ASM International.
- Introduction to Spinning Process - Online Clothing Study.
- Process management in spinning Full Book.
- Spinning Process - an overview | ScienceDirect Topics.
- Metal Spinning- Design Consideration and parameter of spinning.
PDF Analysis of tube spinning process - ResearchGate.
Spinning is the process of conversion of textile fibers and filaments into yarns for weaving or knitting into fabrics. In this article, we are going to know about the various processes which lead to the formation of worsted spun yarns. Worsted spun yarns differ from the regular woollen yarn in various properties.
6.9 Synthetic Fibers - US EPA.
Spinning process 1 of 33 Spinning process Sep. 26, 2018 21 likes 5,096 views Download Now Download to read offline Engineering melt, dry, wet spinning process Shubhambsnl Follow Advertisement Recommended chemical spinning Daffodil International University 2.3k views 58 slides Fiber spinning processes Vivek Dave 4.6k views 22 slides. Manual metal spinning is typically performed at room temperature. However, elevated-temperature metal spinning is performed for components with thick sections or for alloys with. Different spinning methods are available in making yarns, including ring-spun, rotor-spun, twistless, wrap-spun and core-spun yarns.. Ring-spun yarns: This is the most widely used method of staple-fibre yarn production. The fibres are twisted around each other to give strength to the yarn. Rotor-spun yarns: These are similar to ring-spun yarns and usually made from short staple fibres.
[PDF] Experimental results and mathematical formulation of.
ROTOR SPINNING PROCESS 1 of 61 ROTOR SPINNING PROCESS Nov. 08, 2017 52 likes 30,806 views Download Now Download to read offline Engineering This slide contains rotor spinning system briefly. This slide was based on BUTEX syllabus. Mazbah Uddin Follow Student at Bangladesh University of Textiles BUTex Advertisement Recommended Rotor spinning.
PDF Engineering Techniques of ring Spinning - ResearchGate.
Download full-text PDF Read full-text Citations 1 References 9 Figures 4 Abstract and Figures The fibre structure of synthetic filaments is realized during the polymer spinning process. In the present chapter, the solution-spinning processes will be briefly described. Keywords Coagulation Bath Coagulation Rate Cellulose Triacetate Hydraulic Drag Bicomponent Fibre These keywords were added by machine and not by the authors. This process is experimental and the keywords may be updated as the learning algorithm improves. Spinning is the first step of textile product processing. In fact, the process of making yarns from the textile fiber stands for spinning. Accordingly, there are various types of spinning methods for producing different types of yarn. Besides, if we notice, we will see that the cotton fibers convert into carded yarn, combed yarn, and rotor yarn.
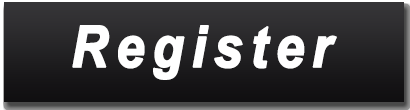
PDF RING SPINNING | ders deers - A.
Step 7: Wind On. Your freshly spun yarn will eventually get too long to keep adding to comfortably. Unhook the yarn and wind all but 10#x27; or so around the shaft of your spindle, then bring it around the whorl and into the hook again. Now continue with the quot;park and draftquot; method. Add Tip. Spinning is the act of taking animal fibers or vegetable fibres and twisting them to form a continuous, infinitely stretching yarn suitable for weaving. Simply put, it is the process of spinning fibres into yarn by mechanical.
Cotton Yarn Spinning Process Step by Step - Textile Learner.
Textile Spinning - Complete Textile Solutions - Texcoms Worldwide. This is so that, by the end of the stroke, there is no pressure at all. Short strokes, in a back and forth sweep feathered stroke, will ensure the elimination of minor wrinkles in the metal. It can also help with over stretching. Spinning is the process of taking textile fibers and filaments and making them into yarn. For thousands of years, people spun natural fibers into yarn by hand. Today, spinning involves many.
PDF The Rieter Manual of Spinning.
The process of converting fiber into yarn is called as Spinning. Flow Chart of Spinning: Pic- Carded Yarn flow chart Pic- Combed Yarn flow chart Objectives: Blowroom: Opening: Open the material into very fine tufts Cleaning: Eliminate most of the impurities. Mixing and Blending: Provide a good blend of two different fibers.
PDF Spinning Basics 1 of 7.
. The spinning process of thermotropic LC polymers is typically carried out through conventional melt-spinning extrusion. During extrusion through very small holes, the shear flow induces an alignment of the LC domains in the flow direction: in this way, the extruded fiber is characterized by a highly oriented structure as depicted in Fig. 17.49. Reaction spinning Spandex Rayon viscose process 6.9.2.1 Melt Spinning - Melt spinning uses heat to melt the polymer to a viscosity suitable for extrusion. This type of spinning is used for polymers that are not decomposed or degraded by the temperatures necessary for extrusion. Polymer chips may be melted by a number of methods.
Spinning Process Overview: From Fiber Material to Yarn.
Abstract and Figures Tube spinning is a continuous bulk-forming process used to produce seamless, cylindrical, conical and contoured tubes. Over the last six decades, tube.
Spinning - ASM International.
The Metal Spinning Process. In the basic set-up for a horizontal spinning lathe the tool mandrel chuck is mounted to the headstock of the lathe. A follower block tail block is mounted to the tailstock. A circular blank is then clamped to the tool by advancing the follower. The tool rest and pin provide a support system for the lever arms, a. Spinning Basics Page 7 of 7 Pedaling in circles utilizes both legs during the pedal stroke and eliminates the deadweight of the upstroke leg. You do this by acting as if you are trying to quot;scrape mud off the bottom of your shoequot; as the foot reaches about the 6 o#x27;clock position as shown in this figure of the Pedal Cycle starting at.
Introduction to Spinning Process - Online Clothing Study.
Reaction spinning Spandex Rayon viscose process 6.9.2.1 Melt Spinning - Melt spinning uses heat to melt the polymer to a viscosity suitable for extrusion. This type of spinning is used for polymers that are not decomposed or degraded by the temperatures necessary for extrusion. Polymer chips may be melted by a number of methods. Spinning is a sheet metal forming process in which a metal blank is pressed over a rotating chuck or form mandrel with the help pressing tool to obtain axisymmetric hollow shell. The sheet metal parts that have circular cross-section can be made by this process. First stage of Spinning involves converting lightly compressed Cotton bales into the form of Opened and Cleaned Fiber Flocks. Blow Room At this process the Fibers in Bale form will be loosen, opened and cleaned. This is the starting stage of Spinning Process. There are three actions happen in Blow room machine. They are; Action of Opposing Spikes.
Process management in spinning Full Book.
There are 3 main process parameter are consider for spinning process. These process parameter are as follow 1. Workpiece Parameters a. Blank thickness b. Blank Diameter c.. Spinning process allows for the rapid production of multiple parts as well as quick reiteration since only the one tool the mandrel need be modified. Depending on the complexity of the. Spinning is the process where yarn is Produced from raw cotton. Severel process and machineries are involved with this industry. Spinning is the initial process for fabric or ready made garments production. Download Free PDF Related Papers Tanveer Hussain Download Free PDF View PDF Fahim Anik Download Free PDF View PDF Ahmad Mukhtar.
Spinning Process - an overview | ScienceDirect Topics.
In most cases, forward tube spinning process is usually adopted to manufacture thin-walled tubular components with a high length- diameter ratio [7]. In this spinning process, however, flaring may occur at the opening end of workpiece Fig. 2 [810]. This can easily lead to fracture at the tube end in the subsequent spinning process. This demands a detailed study on the effect of spinning process variables on fibre orientation and properties of products produced out of these machines. This paper reports a glimpse on the. On the contrary, ring spinning is deemed to be the most widely used spinning system because of its versatility in producing low-twisted soft, absorbent yarn for knitting to.
Metal Spinning- Design Consideration and parameter of spinning.
COTTON SPINNING PROCESS FLOW CHART PDF gt;gt; READ ONLINE COTTON SPINNING PROCESS FLOW CHART PDF spinning process ppt types of spinning process spinning process step by step cotton spinning process pdf cotton yarn manufacturing process pdf. Process Flow Chart of Melt Spinning. Feeding Polymer chips. . Melting. . Metered extrusion. . Rotor spinning process and its properties. Continual improve-ments in spinning elements and conditions make it now pos-sible to spin a rotor yarn optically similar to a ring-spun yarn. Volume 6 - Alternative Spinning Systems To take full advantage of alternative spinning systems, a thorough understanding of them is therefore essential. This. A STUDY ON DEEP DRAWING AND SPINNING PROCESS IN SHEET METAL. PDF Metal Forming By Sheet Metal Spinning Enhancement of Mechanical. Materials used in the spinning process include non-alloyed carbon steels, heat-resistant and stainless steels, non-ferrous heavy metals and light alloys. The process is capable of forming a workpiece with a thickness.